Introduction
Microfluidic technology has revolutionized the way researchers manipulate and analyze fluids at the microscale, offering unprecedented control and precision. Custom microfluidic chips, tailored to specific experimental needs, play an important role in advancing research in fields ranging from biology to chemistry. In this blog, we’ll walk you through the process of crafting your own custom microfluidic chips, from design to fabrication.
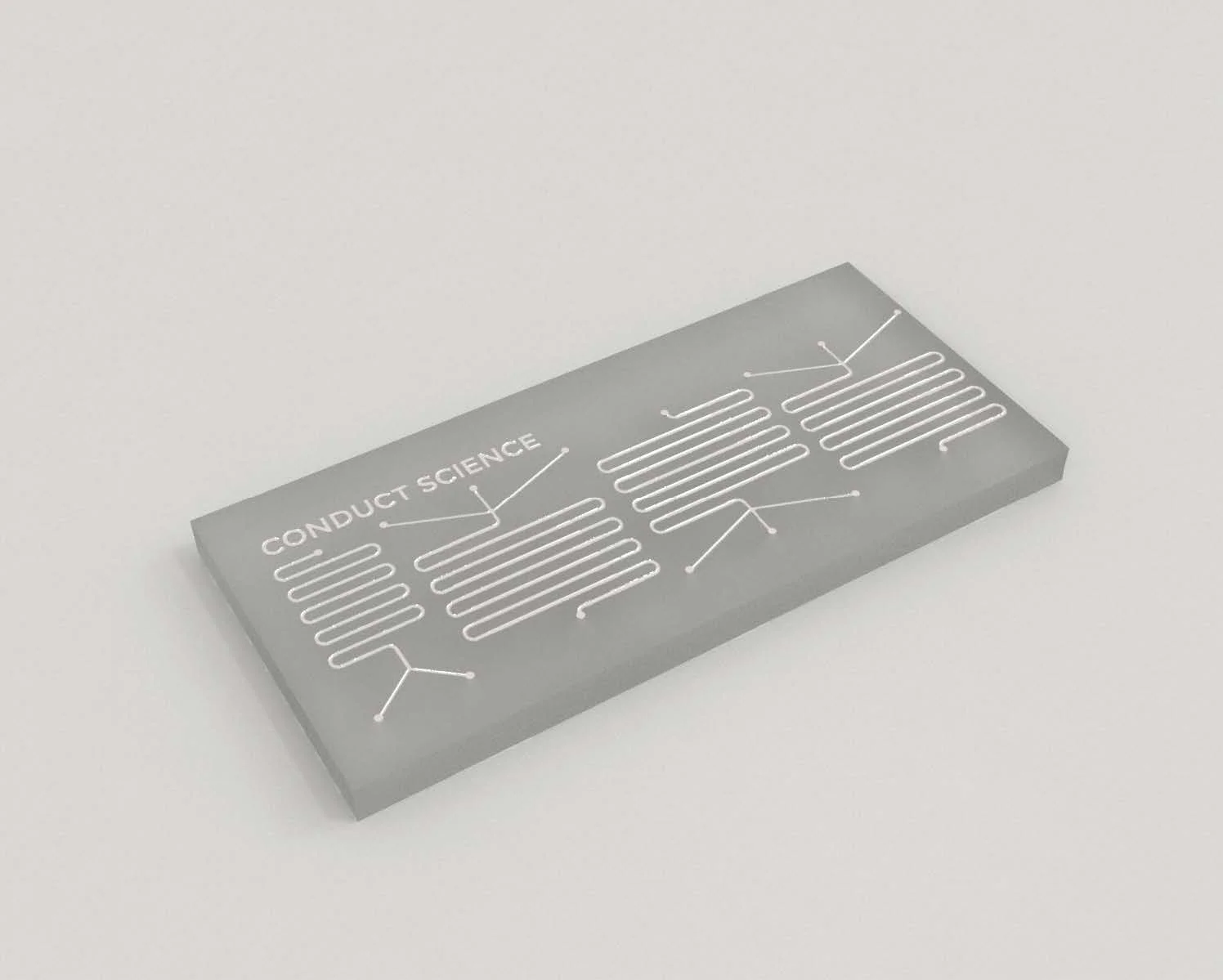
Figure: Microfluidic Chip
1. Designing Your Microfluidic Chip
The first step in creating a custom microfluidic chip is designing its layout. This involves deciding on the dimensions, shapes, and connectivity of the microfluidic channels and chambers. Software tools such as AutoCAD, Adobe Illustrator, or specialized microfluidic design software like L-Edit or CoventorWare can be used for this purpose. Considerations such as fluid flow rates, mixing efficiency, and compatibility with fabrication techniques should guide your design choices [1].
2. Choosing the Right Material
Selecting the appropriate material for your microfluidic chip is crucial. Common materials include glass, silicon, and various polymers such as polydimethylsiloxane (PDMS) and polymethyl methacrylate (PMMA). Each material has its advantages and limitations in terms of optical transparency, biocompatibility, and fabrication complexity. Consider the specific requirements of your experiment when choosing the material for your chip [2].
3. Fabrication Techniques
Once you have finalized the design and chosen the material, it’s time to fabricate your custom microfluidic chip. Several techniques are commonly used for this purpose:
- Photolithography: A photomask is used to transfer the chip design onto a substrate coated with a photosensitive material. Ultraviolet (UV) light is then used to expose and develop the pattern, creating the microfluidic channels and structures.
- Soft Lithography: Soft lithography techniques, such as replica molding and microcontact printing, involve casting a replica of the desired microfluidic structure using a flexible mold made from materials like PDMS. This approach is particularly suitable for rapid prototyping and low-cost fabrication.
- 3D Printing: Additive manufacturing techniques, such as stereolithography (SLA) or digital light processing (DLP) 3D printing, can be used to directly fabricate microfluidic structures layer by layer. 3D printing offers versatility in design and enables rapid iteration of complex geometries.
Laser Micromachining: Laser-based techniques, such as laser ablation and laser cutting, can be used to directly sculpt microfluidic channels and features on various substrates. These techniques offer high precision and are well-suited for fabricating custom microfluidic chips with intricate designs [3].
4. Assembly and Integration
Once the microfluidic structures are fabricated, they may need to be assembled and integrated with other components, such as connectors, valves, and sensors, depending on the specific application. Bonding techniques such as plasma bonding, thermal bonding, or adhesive bonding may be employed to seal the microfluidic channels and ensure leak-free operation [4].
5. Testing and Validation
Before deploying your custom microfluidic chip for experiments, it’s essential to thoroughly test and validate its performance. Conducting flow tests, evaluating mixing efficiency, and assessing biocompatibility are some of the key steps in this process. Iterative refinement of the design and fabrication parameters may be necessary to optimize the chip’s performance for its intended application [5].
Conclusion
Crafting custom microfluidic chips is a multidisciplinary endeavor that combines principles from engineering, physics, and biology. By following the steps outlined in this guide and leveraging the diverse fabrication techniques available, researchers can create tailor-made microfluidic platforms to address a wide range of scientific questions and challenges.
Start exploring the possibilities of custom microfluidic chip fabrication today and unlock new opportunities for innovative research and discovery. Get the best ones at ConductScience! https://conductscience.com/lab/custom-microfluidic-chips/
References
- Duffy, D. C., McDonald, J. C., Schueller, O. J., & Whitesides, G. M. (1998). Rapid prototyping of microfluidic systems in poly(dimethylsiloxane). Analytical Chemistry, 70(23), 4974–4984.
- Berthier, J., & Beebe, D. J. (2014). Flow rate analysis of a surface tension driven passive micropump. Lab on a Chip, 4(4), 371–377.
- Melin, J., & Quake, S. R. (2007). Microfluidic large-scale integration: The evolution of design rules for biological automation. Annual Review of Biophysics and Biomolecular Structure, 36(1), 213–231.
- Qin, D., Xia, Y., & Whitesides, G. M. (2010). Soft lithography for micro-and nanoscale patterning. Nature Protocols, 5(3), 491-502.
- Carrilho, E., Martinez, A. W., Whitesides, G. M. (2009). Understanding wax printing: A simple micropatterning process for paper-based microfluidics. Analytical Chemistry, 81(16), 7091–7095.
- Han, Yong & Jiao, Zeheng & Zhao, Jingjing & Chao, Zixi & You, Zheng. (2021). A simple approach to fabricate multi-layer glass microfluidic chips based on laser processing and thermocompression bonding. Microfluidics and Nanofluidics. 25. 10.1007/s10404-021-02479-y.
Author:
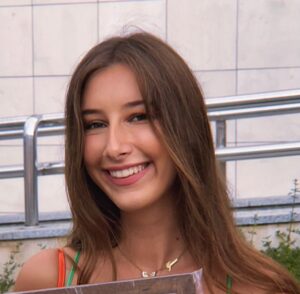
Vanja Antonijevic
Vanja works as the Social Media and Academic Program Manager at Conduct Science. With a Bachelor's degree in Molecular Biology and Physiology and a Master's degree in Human Molecular Biology, Vanja is dedicated to sharing scientific knowledge on social media platforms. Additionally, Vanja provides direct support to the editorial board at Conduct Science Academic Publishing House.